IQT Totally Automated Laboratory Model
Model: IQT TALM
As a technology leader, the IQT system was the first CVCC instrument to market, with the initial system being sold in 1998. As the referee test method in EN 15940, the paraffinic fuels specification in Europe, the IQT system continues to be a proven, reliable, and precise instrument with low operating costs; attributable to small sample size, lower specification combustion air, and low cost reference materials. The precision and accuracy of the IQT also make it a powerful tool for fuel blending and research purposes. With over 200 instruments installed worldwide, some with over 100,000 test runs, the IQT has a proven and trusted track record.
The CFR IQT is the specified equipment for testing fuels according to:
ASTM D6890: Standard Test Method for Determination of Ignition Delay and Derived Cetane Number (DCN) of Diesel Fuel Oils by Combustion in a Constant Volume Chamber covering the range of 31.5 to 75.1 DCN.
EN 15195 (IP 498): Liquid petroleum products – Determination of ignition delay and derived cetane number (DCN) of middle distillate fuels by combustion in a constant volume chamber.
ASTM D6571:Standard Specification for Biodiesel Fuel Blend Stock (B100) for Middle Distillate Fuels
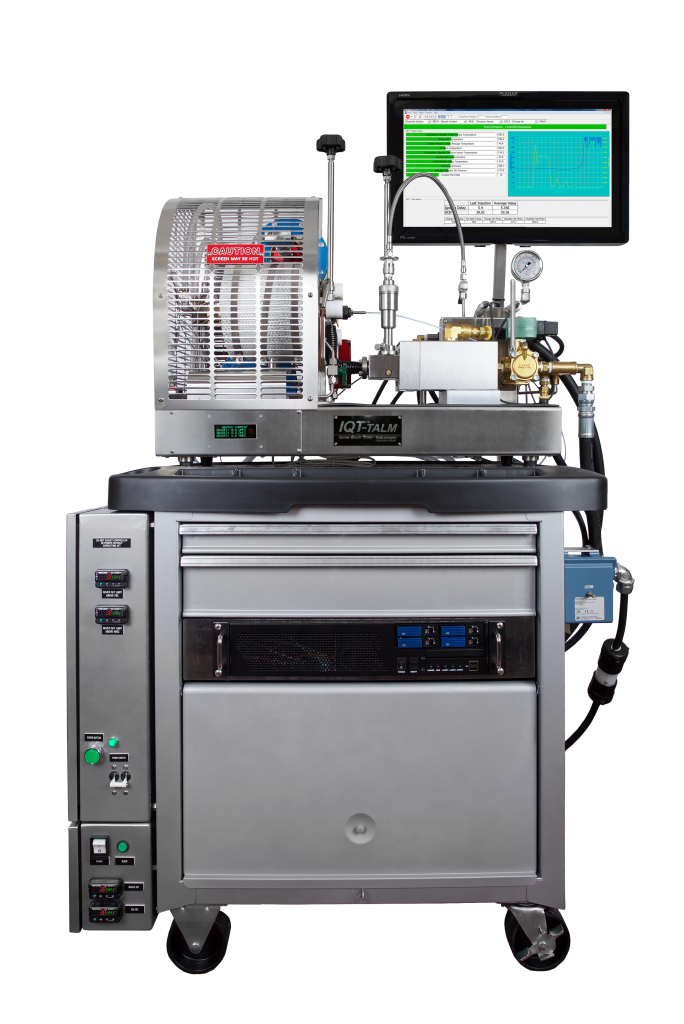
IQT Information Brochure
TALM Precision Package
The IQT TALM system builds upon the standard LM system and adds upgrade kits to improve automation, precision, and ease of use. A total of 8 TALM upgrades are available to offer users flexibility in their system design. Furthermore, a single TALM Precision Package can be ordered, which combines the 5 primary TALM kits that contribute to improved precision.
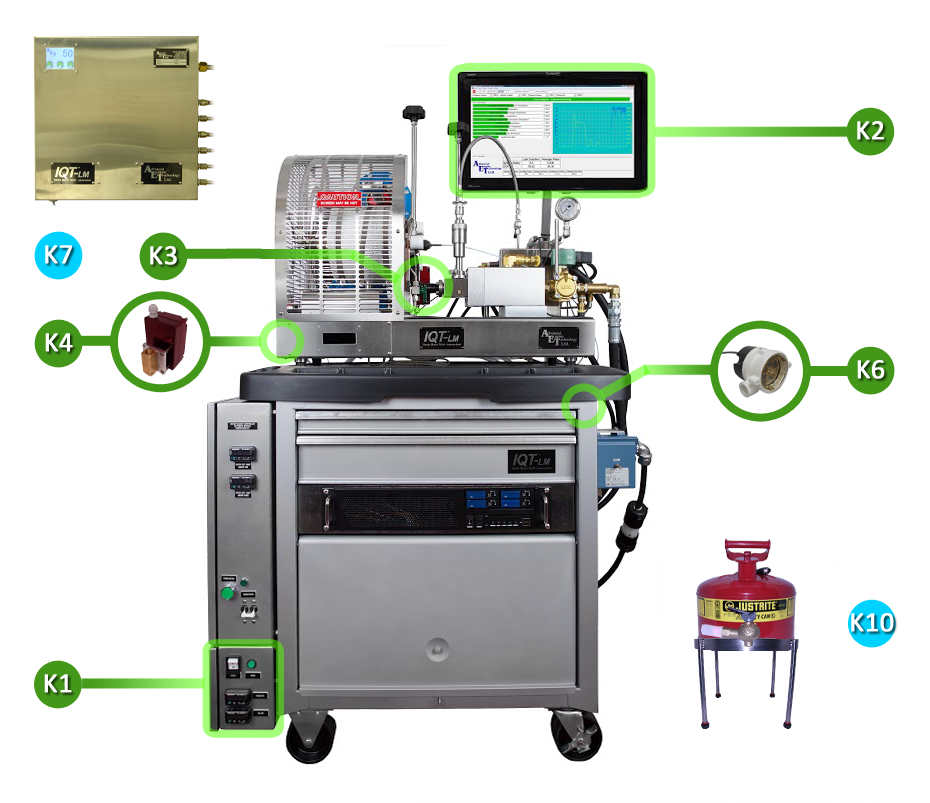
Precision Package Kits (K1 – K4, K6)
TALM-K1: System Control Cabinet
Provides the electronics interface for other automated components
(required for kits K3 – K6, K10)
TALM-K2: IQT System and Control Software
The IQT TALM software user interface allows improved high visibility test monitoring for viewing from anywhere in a lab environment. The software provides an automated calibration option, in unattended mode, enhancing testing productivity and ease of use.
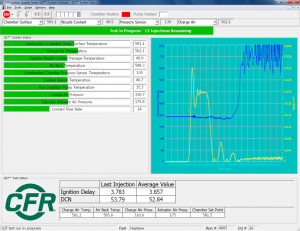
TALM-K3: Nozzle Tip Temperature Control
Improves the precision of the IQT and removes the need to manually adjust the flow of coolant through the nozzle tip
(Requires TALM K1 and K2 kits)
TALM-K4: Combustion Chamber Tail Temperature Control
Improves the precision of the IQT™ and removes the need to manually adjust the flow of coolant through the combustion chamber tail
(Requires TALM-K1 and K2 kits)
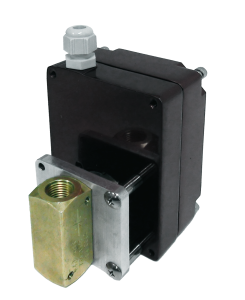
TALM-K6: Electronic Coolant Flow Indicator
Alerts the operator of coolant flow abnormalities. This removes the need to manually check the flow indicator at the start and end of an operating period. TALM kit K6 offers automated digital indication of coolant flow within IQT™ System Software (ISS)
(Requires TALM-K1 and K2 kits)
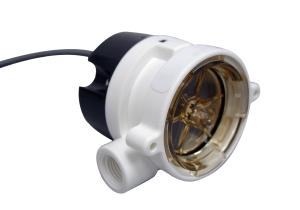
Additional TALM Upgrade Kits
TALM-K7: Electronic Pressure Regulator Panel is optionally available to further improve automation and precision. This system, which controls all three gas stream pressures and also monitors the supply of gas left in each of the cylinders, offers the following benefits:
Eliminates the requirement for the IQT’s operator to periodically adjust the gas pressure regulators.
Improves instrument precision by providing precise and more stable gas pressures than can be achieved using hand operated, mechanical gas pressure regulators.
Warns the operator if one of the IQT’s gas cylinders is almost empty, so that a test is not unexpectedly aborted.
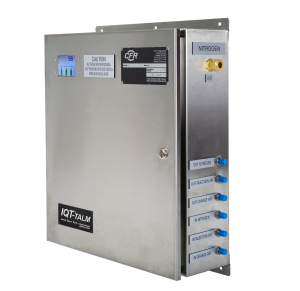
TALM-K8: Improved Heater monitoring tool (coming soon)
TALM-K9: Self Sealing Fuel Reservoirs with Filling Cleaning Station
Provides users enhanced productivity, safer sample handling, and reducing fuel exposure.
Self sealing reservoirs can be filled remotely in a ventilated area and then transferred to the IQT for testing. Samples can be safely prepared in advance for quicker sample changes and increased productivity.
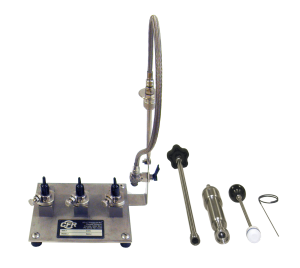
TALM – K10: Waste Fuel Container
Allows automated monitoring of the fuel level in the waste fuel container, avoiding potential spills. Operator alerts are provided through the TALM-K2 graphical user interface.
(Requires TALM-K1 and K2 kits)
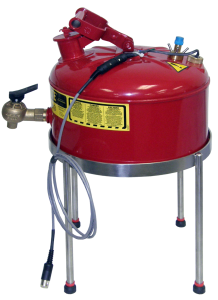
Other Important Features
- ASTM D6890-18 extends the scope over a wider test range: 31.5 to 75.1 DCN, with continued improvements in precision
- Sensitive to cetane improver additives and small fuel quality variations
- Can measure very high levels of cetane improver (3000 ppm+ 2EHN) with no negative carryover effects
- Proven ability to test highly paraffinic fuels from synthesis or hydro-treatment
- Automated test procedure, quiet operation and easy to operate
- Short test time (less than 20 minutes), high productivity; TALM-K9 filling and cleaning station permits multiple fuel samples to be prepared for testing ahead of time through use of multiple fuel reservoirs
- Small sample size (less than 100 mL)
- High level of reliability, rugged system, low operating and maintenance costs
- Easy access for maintenance
- Safety track record established over many years
- Proven testing capability for B100 and other biodiesel fuels from many different sources
IQT Dimensions | 173cm (68 in) H X 106 cm (41.5 in) W X 73 cm (28.5 in) D. |
Power Requirement | 20A, 240VAC, 50/60 Hz Protected by an Uninterruptable Power Supply (UPS) and isolation transformer |
Air Supply | Compressed air, 20.9 % O2 ± 1.0% Regulated: 21.7 bar (310 psi) – Combustion process 12.1 bar (175 psi) – Injection process |
Nitrogen Supply | Compressed nitrogen, industrial grade Regulated: 3.5 bar (50 psi) – Fuel feed process |
Cooling System | Closed-circuit liquid to air cooling system |
Fuel Injection System (Patent Pending) | Pintle-type, single hole nozzle with pneumatically actuated fuel injection pump |
Computer and Instrument Control | Rack mount computer system with automatic software backup and hot-swappable drives |